Este minicurso será dividido em duas partes, sendo:
9h às 13h - API Short Course on Fitness-For-Service
13h às 17h - API Short Course on Risk-Based Inspection
os dois minicursos terão tradução inglês x português x inglês
9h às 13h
Título: Minicurso API Short Course on Fitness-For-Service
This short course on Fitness-For-Service provides the student with a basic understanding of API 579-1/ASME FFS-1 and the types of assessments that can be performed using the standard. FFS procedures enable users to assess the mechanical integrity of equipment and make projections about remaining useful life. The procedures in API 579-1/ASME FFS-1, which are specifically prepared for equipment in the refining and chemical process industries, can be used to make run-repair-replace decisions. This is needed to ensure the safe operation of pressurized equipment that may have flaws or damage identified through inspection.
The FFS Short Course is aimed primarily at plant reliability management, inspectors and engineers that desire an overview of the FFS assessment process, rather than an in-depth course on the evaluation of specific damage.
Instrutor: Joel Andreani (E2G)
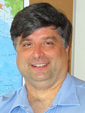
Minicv:
Mr. Andreani performs Fitness-For-Service evaluations, engineering specification and design support, engineering training, and project consulting on a wide variety of refinery and chemical plant equipment. A pressure-containment and structural specialist, Mr. Andreani has worked in various refinery technical service groups providing engineering support to refineries and chemical plants worldwide.
Mr. Andreani has developed advanced skills in Finite Element Analyses with emphasis on non-linear behavior. He performs advanced stress analysis in the design and assessment of tankage and spheres, piping, pressure vessels, steel and concrete structures, and foundations. He appraises the service suitability of existing equipment in accordance with API 579. He is also an expert in tank settlement, having been one of the primary developers of API 653 edge settlement procedures, and the leader of a current API project to re-write API 653 rules on differential shell and global bottom settlement. He analyzes vibration of equipment and structures, and performs fatigue assessments, structural reliability evaluations and risk assessments.
Mr. Andreani has managed company specification programs and has developed over 50 design, fabrication, inspection and testing specifications for tankage, piping and structures, and specifications for wind, seismic and blast load criteria for petrochemical equipment and structures for petrochemical facilities worldwide. He performs design reviews for tankage, piping, pressure vessels, structures and foundations as part of major refinery capital projects, including expansions, revamps and de-bottlenecking projects. In addition, Mr. Andreani serves on the API Aboveground Storage Tank Subcommittee on Design, and performs code compliance calculations and interpretations for tankage, piping, pressure vessels, structures and foundations.
13h às 17h
Título: Minicurso API Short Course on Risk-Based Inspection
Objetivo: This short course on Risk-Based Inspection provides the student a basic understanding of API 580, which provides minimum guidelines for developing a RBI program, and API 581, which gives details of one method for quantitative RBI. Together, these two documents comprise a widely-recognized standard for industry-accepted RBI practices. The API Risk-Based Inspection (API RBI) methodology is used to manage the overall risk of a plant by focusing inspection efforts on the process equipment with the highest risk. The results of a RBI study help plant personnel make more informed decisions and target inspection resources where they are needed most.
The RBI Short Course is aimed primarily at plant reliability management, inspectors and engineers that desire an overview of RBI, rather than an in-depth course on the RBI process.
Instrutor: Phil Henry (E2G)
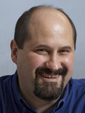
Minicv:
Mr. Henry is responsible for engineering consulting services in the areas of Pressure Relief, Heat Transfer and Fluid Flow. He is a specialist in the design, installation, sizing and selection of pressure relief devices and relieving systems, and is currently chairman of the API Pressure Relieving System Subcommittee’s Task Force on API 520 related to the design and installation of pressure relieving systems. He conducts audits of pressure relieving systems to ensure compliance with OSHA PSM legislation and ASME, API and DIERs Standards, Codes and Publications. He also teaches the official API Pressure Relieving Systems course.
He is actively involved in the development of technology for the API Risk-Based Inspection (RBI) methodology, is co-author of the re-write of API 581, Risked-Based Inspection Base Resource Document. He has been responsible for the development and implementation of RBI programs for pressure relief valves and heat exchanger bundles at many refining and petrochemical plants.
Mr. Henry is also an expert in the area of mechanical and thermal design of unfired heat exchangers, including troubleshooting of performance problems, fouling evaluation, network optimization and pinch analysis, mechanical vibration and field performance testing. He performs steady state and transient hydraulic evaluation of piping systems, including multi-phase flow systems, and develops bolting procedures for flanged joints including use of hydraulic torquing, tensioning, and ultrasonic elongation equipment. Mr. Henry has significant experience with the design and analysis of in-service fixed equipment. He has been responsible for rerating vessels to the ASME Code and NBIC and has applied FFS assessments in accordance with API 579. He has provided problem-solving support during numerous refinery shutdowns.

|